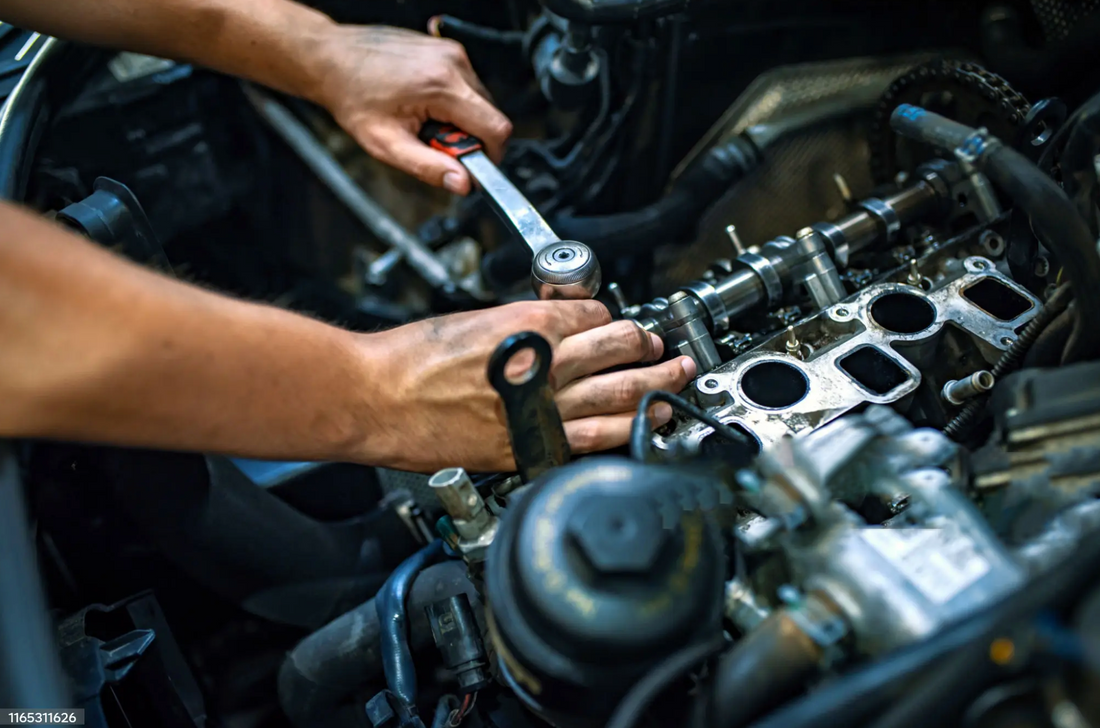
The Ultimate Guide to Spare Parts Inventory
MUHAMMED NAJEEBShare
Understanding Spare Parts Management
Spare parts management can keep equipment running smoothly. It involves stocking and tracking replacement components to fix broken machines quickly.
Importance of Spare Parts in Maintenance
You need working spare parts to fix equipment quickly. Having the right parts on hand lets maintenance teams make repairs immediately, keeping production going and saving money.
Critical spare parts need special attention. These are components that will shut down operations if they fail. Stocking them is a must to avoid costly delays.
Regular parts are also important. They prevent minor issues from turning into big problems. A good stock of common parts helps maintenance run smoothly.
Challenges in Spare Parts Management
Spare part management can be tricky. One big issue is deciding what to stock and how much.
Too few parts can lead to long repair delays, but too many waste money and space. It is important to find the right balance.
Tracking parts is another challenge. Organizing the spare parts area is crucial. Parts must be easy to find when needed.
Keeping data up to date is also challenging. Part numbers, locations, and quantities change often, and good systems are needed to keep information correct.
Predicting part needs is tough, too. Usage patterns can shift with equipment age and conditions.
Inventory Management Fundamentals
Effective spare parts management relies on solid inventory control practices. Balancing stock levels with costs is key to optimizing operations.
Stock Levels and Lead Times
Computerized systems help track and manage parts inventory. These tools monitor stock levels and reorder points. They alert managers when supplies run low.
Lead times affect inventory decisions. Parts with long lead times may need higher stock levels. This prevents stockouts during critical repairs.
Safety stock acts as a buffer against demand spikes. It protects against supply chain disruptions. The right amount depends on part criticality and usage patterns.
Demand forecasting improves inventory accuracy. It uses historical data and trends to predict future needs.
This helps prevent overstocking or understocking of spare parts.
Inventory Cost Considerations
Holding costs include storage, insurance, and depreciation. These increase with larger inventories. Managers must balance holding costs against stockout risks.
Ordering costs cover purchasing and receiving parts. Frequent small orders increase these costs. Bulk orders may reduce per-unit costs but tie up more capital.
Centralized storage can lower overall inventory costs. It improves accuracy and accessibility. This approach often reduces duplicate stock across locations.
Obsolescence is a major cost risk for spare parts. Slow-moving items may become outdated before use. Regular inventory turnover reviews help identify at-risk parts.
Challenges in Spare Parts Management
Spare part management can be tricky. One big issue is deciding what to stock and how much.
Too few parts can lead to long repair delays, but too many waste money and space. It is important to find the right balance.
Tracking parts is another challenge. Organizing the spare parts area is crucial. Parts must be easy to find when needed.
Keeping data up to date is also challenging. Part numbers, locations, and quantities change often, and good systems are needed to keep information correct.
Predicting part needs is tough, too. Usage patterns can shift with equipment age and conditions.
Leveraging Technology in Spare Parts Management
Implementing modern technologies can help simplify spare parts management. It helps companies track inventory, plan maintenance, and make smart decisions about parts.
Computerized Maintenance Management System (CMMS)
CMMS software is a powerful tool for spare parts management. It helps track parts, schedule maintenance, and manage work orders.
CMMS systems store data on:
Part numbers and names
Quantities in stock
Locations of parts
Costs and suppliers
Usage history
This data helps managers:
Order parts at the right time
Avoid stockouts and excess inventory
Plan maintenance tasks better
CMMS also tracks equipment history. This lets teams see which parts fail often and plan.
Inventory Tracking Technologies
New tech makes tracking spare parts easier and more exact. Automated systems like barcode scanners and RFID tags help count and locate parts fast.
Barcode systems:
Speed up part check-in and check-out
Reduce human errors in data entry
Update inventory counts in real-time
RFID tags go further:
Track parts without line-of-sight
Monitor part movements automatically
Work well in harsh settings like warehouses
These tools give a clear view of stock levels. Managers can set alerts for low stock and track part usage trends. This leads to better forecasting and less waste.
Identifying and Managing Critical Components:
Critical spares are parts needed to fix equipment quickly and avoid extended shutdowns. Common examples include bearings, motors, circuit boards, and valves. To identify critical spares, companies should:
• Review equipment failure history
• Consult with maintenance staff
• Consider lead times for replacements
• Assess impact on operations
Once identified, critical spares need proper management. This involves:
• Tracking inventory levels
• Setting reorder points
• Storing parts correctly
• Regular inspections
Using maintenance management systems can help organize and monitor critical spare parts. These tools provide real-time visibility into inventory and automate reordering processes.
Optimizing Critical Spare Parts Inventory:
Balancing inventory levels is key for effective critical spare parts management. Keeping too many parts ties up capital, while too few risk downtime. To optimize inventory:
• Analyze usage patterns
• Use data to forecast demand
• Set minimum and maximum stock levels
• Consider pooling parts across facilities
Critical spare parts management may also involve:
• Partnering with suppliers for quick deliveries
• Exploring refurbishment options
• Using predictive maintenance to reduce part needs
Regular audits help ensure the correct parts are on hand. This protects against obsolescence and identifies opportunities to reduce excess stock.
Best Practices and Compliance
Good spare parts management keeps equipment running smoothly and helps companies follow important rules. Let’s look at key ways to manage spare parts well and stay compliant.
Spare Parts Management Best Practices
Using software to track parts is a top practice. A Computerized Maintenance Management System (CMMS) helps monitor inventory. It shows what parts are in stock and when to order more.
Having a clear work order process is crucial. This means deciding who starts work orders and how to label parts. It also includes getting supervisor approval when jobs are done.
Controlling inventory is key. Companies should:
Keep only needed parts on hand
Store parts in a clean, organized space
Check stock levels often
Use data to predict when parts will be needed
Training staff on proper parts handling improves quality. It helps avoid damage and ensures parts work when needed.
Compliance with Industry Regulations
Following rules keeps operations safe and legal. Companies must know which regulations apply to their industry. Common areas include:
Safety standards for storing and handling parts
Environmental rules for disposing of old parts
Quality control measures for critical components
Regular audits help ensure compliance. These checks can find issues before they become big problem
Proper documentation is a must. This includes keeping records of:
Parts purchases and usage
Maintenance activities
Safety inspections
Companies should stay up-to-date on changing regulations. This might mean joining industry groups or working with compliance experts.
Final Thoughts on Spare Parts Management:
Proper inventory storage prevents damage and makes parts easily accessible when needed. This ensures quick repairs and minimizes equipment downtime.
Balancing stocking levels is key. Too little inventory can lead to costly delays, while excess inventory ties up capital and storage space. Regular analysis helps determine the right balance.
Effective spare parts management contributes to extended equipment lifespan. Regular maintenance and timely repairs, facilitated by readily available parts, keep the machinery running smoothly for longer.